
OUR CAPABILITIES
-
Specs: Four-High Reversing Mill, 2,500 tons separating force, 30’ entry/exit tables, capable of rolling to 39” width, maximum starting billet thickness 6”
-
RAD (NU & DU) & Non-RAD (Metal Matrix Composites, Tantalum, Niobium, Molybdenum, and Titanium) Rolling
-
Hot and Cold Rolling
-
R&D and Production Rolling capabilities
-
Development of rolling schedules for R&D
-
Staff, with over 35 years of experience, in the metals fabrication industry
-
Supporting Ancillary Equipment: Salt Bath capable of operating temperatures up to 750 C, Preheating Furnaces capable of operating temperatures up to 1,375 C, Vacuum Heat Treat Furnace with operating temperatures up to 750 C, Annealing and Quenching
-
1/2 Day & Full Day Rolling Rates Available
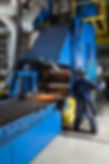
BACKGROUND
Metal rolling is one of the most important manufacturing processes in the modern world. The large majority of all metal products produced today are subject to metal rolling at one point in their manufacture. Metal rolling is often the first step in creating raw metal forms. The ingot or continuous casting is hot rolled into a bloom or slab, these are the basic structures for the creation of a wide range of manufactured forms.
MSC's commitment to quality has never wavered and we continuously strive to maintain the highest accuracy standards through the use of check fixtures and innovative measuring equipment designed specifically for roll bent parts. If your design requirements include any non-stock shapes contact us today!

SPECIALTY METAL ROLLING
